Compressed Air Dryers : your guide (final one!)
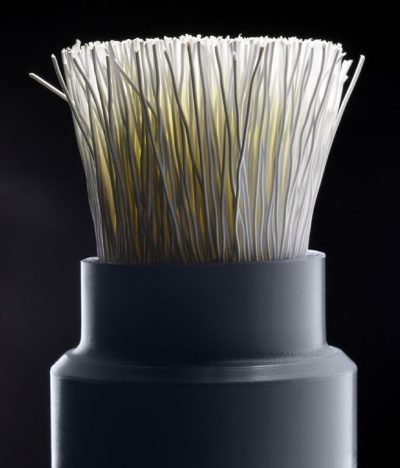
Membrane air dryers
The final type of air dryer for your compressor, is the membrane air dryer. As the name indicates, it runs incoming air over thousands of hollow fibres to rid it of moisture.
The air builds up on the membrane until it migrates through to the other side, which is low pressure. A dry gas is then run through, carrying the moisture away for expulsion.
The performance of a membrane air dryer and its dew point depend on the temperature of the incoming air. Although a proper setup will result in incredibly low dew points. They are often a second or even third stage dryer.
Why choose a membrane air dryer?
Membrane air dryer and filter sets are a popular choice for medical use thanks to the low dew point in a controlled environment resulting in small amounts of high-quality air. They will provide clean, dry air in environments with strict safety or environmental requirements such as noise and corrosion sensitive areas, areas without electrical supply and locations with explosion proof requirement. If you need an air dryer for a laboratory, dentist’s office or hospital, these can be an ideal low-cost solution.
Reasons to go for a membrane air dryer
- These systems are convenient to use, more cost-effective, and require less maintenance since they have no moving parts.
- Operate continuously without using electricity
- Quiet and dependable
- High-quality air compression
- In need of a point-of-use air dryer for industrial use? Then the desiccant dryer is more likely to fit your needs.
Get support from Air4U to make sure you can trust your choice.
If you would more information or advice, please do not hesitate to follow the link to send us an email at sales@air4ultd.co.uk
Compressed Air Dryers : your guide continued
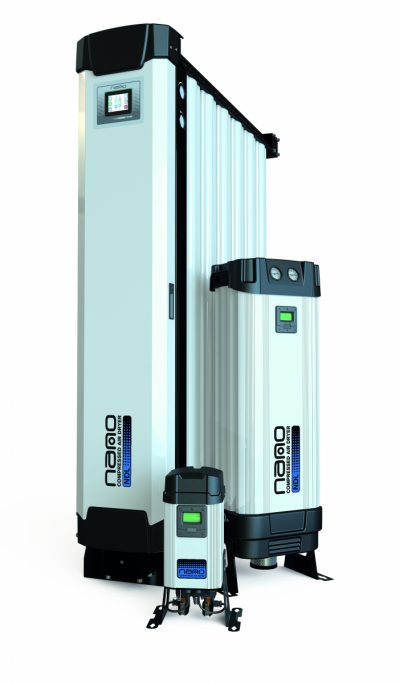
Desiccant air dryers are the next type of Compressed Air Dryers we are looking at.
A Desiccant Air Dryer is a type of adsorption air dryer system. They use a porous hygroscopic medium like activated alumina and silica gel to extract moisture from the air and dry it. Adsorption dryers are used when the compressed air application requires a pressure dew point below 0°. The pressure dew point they can achieve can be sized to produce dew points from -20°C to as low as -70°C
Desiccant Air Dryers are better suited for second stage drying as the hygroscopic medium would otherwise get saturated too quickly. That means they are often the second step after a primary dryer like a refrigerated dryer.
There are 2 main types of desiccant air dryer:
Single canister dryers
These are most often used for point-of-use applications. It contains a granular hygroscopic medium through which the air is pushed and where it is filtered of moisture. Single canister dryers are easy to use and efficient in their energy use.
Twin tower desiccant air dryer
The regenerative desiccant dryers consist of two pressure vessels. Both vessels are filled with desiccant.
The first vessel is removing moisture from the compressed air. Wet air passes directly through the desiccant bed which adsorbs the moisture. When this vessel is saturated with moisture, the valves will switch and lead the air to the other standby vessel. During adsorption in the other vessel, the first vessel will be regenerated. It's a cyclic process.
The desiccant medium has a limited capacity for adsorbing the moisture in your compressed air supply before it must be dried out or regenerated. To do this, the tower containing the saturated desiccant medium is depressurized and the accumulated water is driven off. How this happens depends on the type of dryer.
A heatless desiccant dryer loses about 20% of output to purge. This is because if a desiccant dryer experiences a high pressure drop, the compressor discharge pressure must be set higher, which increases energy and operating costs. Therefore, it is important to select desiccant dryers that offer an exceptionally low pressure drop – below 0.2 bar for most models – as well as the most efficient regeneration process.
A zero-purge desiccant dryer does not lose any of its air output to purge and could save 20% in energy compared to a heatless desiccant
Why choose a desiccant air dryer?
- The regenerative nature and low dew point of desiccant dryers, make it perfect to compress air at or below the freezing point.
- Some advantages of a desiccant air dryer
- Easy to maintain and clean
- Perfect for second stage drying
- Versatile and capable of exceptionally low dew points
Next Up will be Membrane Air Dryers.
Get support from Air4U to make sure you can trust your choice.
If you would more information or advice, please do not hesitate to follow the link to send us an email at sales@air4ultd.co.uk
Compressed Air Dryers : your guide continued
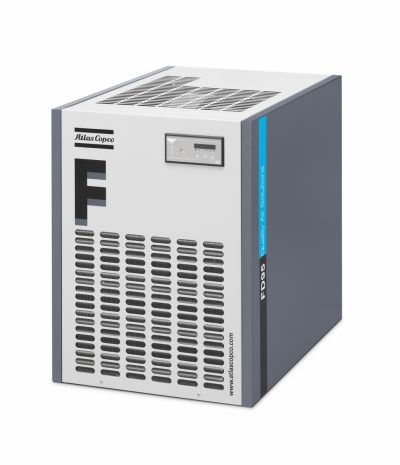
Refrigerated dryers are the most economical drying method for any system.
Refrigeration dryers are used in compressed air systems worldwide and represent the current state of technology. Refrigeration drying is the most cost-effective technology for the drying of compressed air
Refrigerated air dryers operate with a similar principle to domestic refrigerators or home air conditioning systems. Refrigerating air dryers work by cooling the air to low temperatures and condensing the bulk of the water vapour. In other words: it uses temperature differences to remove the water particles. Refrigerated air dryers or refrigerant dryers cool down the air to approximately 3°C or 35°F. At this temperature, known as the dew point, the moisture in the air condenses after which it is drained.
The cooled air is reheated to room temperature upon exiting the dryer and before being used.
The are 2 main subtypes of refrigerant dryers:
Non-cycling refrigerant air dryers continuously refrigerate and thus maintain a consistent temperature. They are very dependable and easy to maintain, but you cannot turn them off. They keep running even if your business is closed.
Cycling refrigerant air dryers produce the amount of cold needed and then shut off until the core temperature reaches a certain level. They automatically turn off and on as needed, making them the more environmentally friendly option. The extra parts needed for this way of working, however, could result in a slightly higher need for maintenance and it does not offer a stable pressure dew point.
Why choose a refrigerated air dryer?
Refrigerated air dryers are the most common type of compressed air dryer. They are perfect for most manufacturing and service applications, provided you just need dry air without any perceptible moisture.
However: water vapour might still remain in the compressed air, so this specific type of compressed air dryer is not to be used in applications that are water sensitive. It can remove a lot of the particles, but not necessarily all of them.
A few benefits of refrigerant air dryers
Cost-effective in purchase and maintenance
Environmentally friendly
Reliable and consistent
Typically, available as a stand-alone product or can be as a built-in full feature option on your air compressor
In need of a compressed air dryer system capable of lower dew points? Then a desiccant air dryer is a better fit for you (see our next blog).
Get support from Air4U to make sure you can trust your choice.
If you would more information or advice, please do not hesitate to follow the link to send us an email at sales@air4ultd.co.uk
Compressed Air Dryers: Your Guide
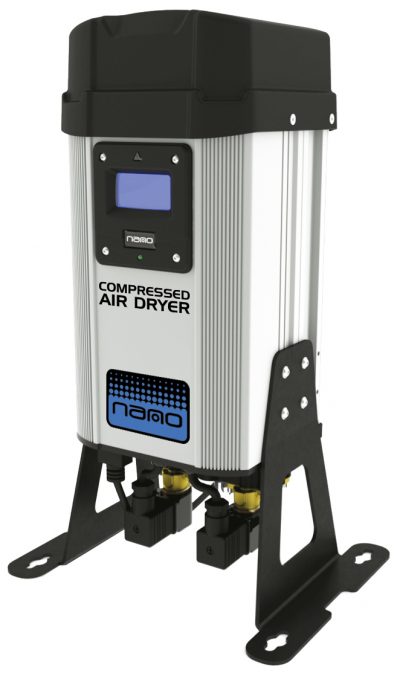
Over the next series of blogs, we will discuss the different types of Compressed Air Dryers and how they work.
In lots of different industrial settings, dry compressed air is essential. In these instances, compressed air dryers are used to make sure the end-product is moisture-free.
The importance of having compressed air dryers
Lots of working environments are particularly water sensitive. Moisture can contaminate the end product and equipment. In particularly cold environments, water particles can also lead to frozen pipes, corrosion, and other important issues. For example, malfunctioning of controls or impairment of tools. This can make you lose time, money, and production quality.
Compressed air dryers are filtering systems that rid your compressed air of moisture created during the compression process. It makes sure that your compressed air is high-quality and free of harmful moisture that could damage your equipment or have a negative effect during use.
Compressed air filters, on the other hand, filter the air from other impurities like dust and gases.
How do compressed air dryers work?
How your compressed air dryer works depends on the type of air dryer you have. Each uses a different technique to produce the same result: providing dry compressed air for your air system to work with.
Essentially, compressed air dryers suppress the dew point of air by removing any remaining water particles. The air that gets compressed can contain moisture that might be harmful to your systems and processes. Especially in pharmaceutical and food industries it’s paramount to have clean, dry compressed air.
How do I choose the right air dryer?
When looking for an industrial air dryer, there are many different models to choose from and it’s easy to get lost. If you follow these tips, you’re on your way to the perfect air compressor and treatment for your business.
- Stick to the air quality you need for your business, no higher or lower.
- Make sure you take into account the longevity of your systems. Investing in high-end systems now will cut down costs tremendously in the long run, saving time and money.
- Get support from Air4U to make sure you can trust your choice.
If you would more information or advice, please do not hesitate to follow the link to send us an email at sales@air4ultd.co.uk
Do you need a Backup Air Compressor?
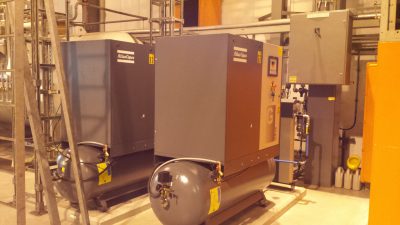
It might not seem to be common sense that reducing total operating costs and increasing the overall reliability of your compressor system could require adding more machinery. If you only have one compressor and that compressor must undergo routine maintenance or you have a breakdown and require emergency service, what happens to your production? It grinds to a halt, leading to costly downtime and a substantial loss in revenue.
Avoid this possibility by investigating a few of the backup options below:
Backup Compressor.
Having a backup compressor eliminates losses of production. If one compressor fails, the backup compressor is ready to be brought into operation.
Lead and Lag.
One compressor is assigned to be the “lead” compressor, while the other is designated as the “lag” compressor. When the lead compressor’s pressure drops to a predetermined point, the lag compressor takes over.
Create Redundancy.
A second air compressor can be linked to operate alongside your main compressor. Both compressors will be sharing the demand, and if the lead compressor fails, the lag unit will continue to operate. This strategy minimizes wear and tear on both units.
Investing in a second compressor is essentially an insurance policy. Your main compressor has a lot of responsibility, so leaving things to chance? Not the wisest option.
Air compressors are highly-engineered products that are essential for production in millions of businesses globally. In fact, compressed air is so critical to these facilities that it is often called the “fourth utility”! Most production cannot function without their utilities such as electric, water, and gas – and it stands to reason that this is also true of compressed air. The cost of downtime of this utility needs to be considered in your air system. Is it important enough to justify a backup unit? Does the backup just sit around and ‘do nothing’?
Are Backup Air Compressors Essential?
The answer is simple: if your business is heavily reliant on compressed air to operate, production will cease, leading to a loss in output, possible production line losses, and costly downtime. Keep in mind that it could be a long time before a compressed air service technician reaches you to complete the repair! And without a backup compressor available for immediate use, the time, money, and productivity lost in the interim between unexpected shutdown and being back up-and-running can be extremely detrimental to the business’ bottom line.
It’s unfortunate, but even the best equipment fails.
This means that having a compressor system, complete with a backup compressor, is absolutely critical. Being proactive and purchasing one now, rather than down the road, is the smartest business decision – especially when you weigh the costs versus consequences of not having one. An additional benefit? Having backup compressors means that maintenance can be done at virtually any point in time, rather than after hours or during the holidays or weekends when production isn’t occurring!
The worry of the compressor sitting and doing nothing can also be eliminated by load sharing. This allows cycling of the compressors to allow even running time for each. Simple controls evenly allot run time allowing each machine to spread the work and maintenance cycles more efficiently for your business while still protecting production uptime.
So, to summarize, the reasons that you need a backup air compressor are:
- To minimize any negative impact on production brought on by unexpected downtime.
- Schedule maintenance on your primary compressor at any point in time.
- Using both your primary air compressor and backup air compressor in your application through load sharing.
Essentially, the costs of not investing in a backup air compressor far outweigh the cost of purchasing one, and you can take surprise shutdowns off the worry list. Rest easy and avoid unplanned chaos – discuss investing in a backup compressor today, please do not hesitate to follow the link to send us an email at sales@air4ultd.co.uk
Reducing Pressure Drops in Your System
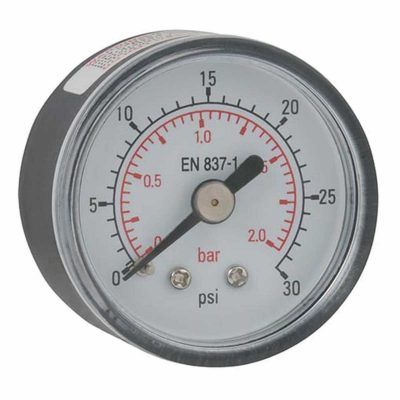
Pressure drops reduce the performance of your compressed air system and cost you money!
There can be many reasons, for example a small leak in your pipework that gets worse over time. They may be tough to spot right away, but eventually you’ll notice a decline in the performance of your system. Pressure drops will lead to an increase in energy consumption and reduce your systems performance.
Pressure drop in a compressed air system is due to airflow resistance caused by pipe friction and various components within the system (e.g., valves, bends). Inadequate pipe sizing also results in pressure drop. The compressor must produce air at a pressure high enough to overcome these pressure losses in the system and still meet the minimum operating pressure of the end use equipment or process. For a compressor delivering air at a pressure of 8 bar, if the pressure at the point of use is say 6.5 bar, this pressure drop of 1.5 bar through the system represents wasted energy and money.
In a properly designed and installed system, pressure drop should be less than 10% of the compressor’s discharge pressure, as measured from the compressor outlet to the point of use. So, at a pressure of 7 bar, the pressure drop should be less than 0.7 bar. The need to generate at a substantially higher pressure than required by the end use application is usually an indication of a pressure drop problem. If reducing the pressure, make sure the most critical process still has sufficient air to operate.
Check the required pressure and air purity levels with the equipment supplier. For example, blow guns should be regulated down to 2 bar to meet health and safety requirements.
If you suspect that the pressure has dropped on your compressor, there are actions that you can take to restore it to normal function. Also, you can always call an Air4u engineer to perform routine maintenance on your compressor.
Ways to Reduce Pressure Drop
Your air compressor and system consume energy to generate the compressed air and quality you require. If you notice it using more than normal, it could be due to a pressure drop.
Below are a few things to check for as you inspect your compressed air system:
Inspect Pipework & Tubing.
- It’s important to inspect it, to make sure that your distribution remain airtight. By listening to your pipework, you may be able to hear air leaks. So, try running your compressor, but do not use any air tools or equipment.
- A leak may be really quiet, so make sure there’s as little background noise as possible. It’s preferable to check outside working hours.
- Walk slowly around the system listening for hissing or rasping sounds – these are usually sure signs that there is a leak. Make sure you include all joints, flanges and valves in your inspection.
Check for Worn Hoses.
- Kinked or worn-down hoses can lead to air leaks. When you inspect hoses regularly to make sure they’re in prime working condition. You may be able to spot a leak earlier, before the problem worsens. Make sure that none of the hoses in your system are in a stressed position. All connection pieces should be properly sized and tight.
Check Regulators.
- The settings on the pressure regulators may be what is causing the pressure drop, and the increase in energy. You can try resetting it, and if you still experience the drop, it might need to be replaced.
Pipework design.
- The layout of your pipework needs to be looked at. It may be time to reconfigure it and move your most used tools closer to your compressor, so that you can eliminate any extension pieces and reduce the amount of ground that needs to be covered. When you shorten the distance air needs to travel, you improve the efficiency of the system.
If you cannot find the source, it may be time to call for a repair.
The Benefits of Reducing Pressure Drop- Saving money!
If you’re experiencing a pressure drop in the system, you may not notice the difference at first. It may not become apparent until your system is expending a significantly higher amount of energy than previously.
But when you successfully address this problem, you will experience improved performance, reduced, maintenance, and lower operating cost. All of this leads to you being able to focus on core aspects of your business.
Your Air Compressor is a Complex Machine.
It can be incredibly difficult to troubleshoot your compressor, and to know what needs to be fixed. If you’ve looked and cannot identify the source in order to reduce pressure drop, it may be time to contact an experienced Air4U engineer to help you with the problem.
Please Remember
Compressed air can be dangerous and therefore we recommend that you consult an expert if you are in any doubt about how to proceed. Always ensure that the system is completely de-pressurised before attempting any repair.
If you wish to find out any further information or would like to book a service, please follow the link to send us an email at sales@air4ultd.co.uk
Did you know Air4u can carry out a Breathing Air Quality Test?
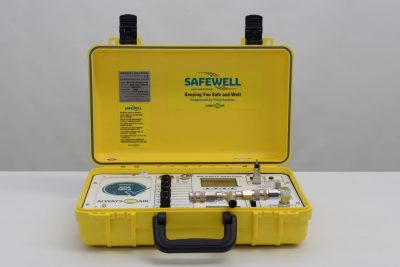
This week, AIR4U staff participated in Breathing Air Quality Test training, where they have learnt or done a refresher, on how to conduct Breathing Air Tests and produce reports.
This is a great service that we can offer our customers. Unlike some of our competitors, we are able to carry out these tests ourselves, without ‘sub contracting’ to a separate company. This ability to control costing means customers using our service should not be paying more than is necessary. Legislation recommends that these tests are carried out every three months. Which can mean increased costs.
At AIR4U, we use the MK2 Air Purity Analyser (APA) which enables us to test and validate the compressed air within your system in accordance with BS EN 12021:2014. The MK2 APA respiratory test takes twenty five minutes, so any Breathing Air downtime, during testing, is kept to a minimum.
For more information, please have a look at our previous blog: https://www.air4ultd.co.uk/is-the-air-from-your-compressor-safe-to-breathe/
If you would like a no obligation quotation on your breathing air test, please follow this link to send us an email: sales@air4ultd.co.uk
AIR4U are delighted to welcome the addition of Jamie Fear to our team
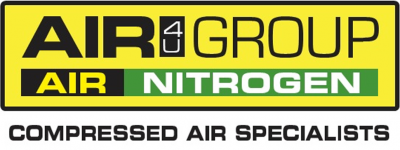
Jamie joins us as Branch Manager having left Southern Air Systems Ltd, where he spent 23 years, along with their team building Southern Air Systems into a well-known service provider.
Jamie started his compressed air career as a service engineer in 1999 and was promoted to Service Manager in 2006. He eventually took on the role of Operations Manager. During this time, he has learnt the fundamentals of compressed air industry and gathered a wealth of knowledge which we hope will be put to great use at Air4u Limited.
We are looking forward to working with Jamie and we are all excited to see what the future brings for Air4u Limited.
What is an Air Compressor Oil Separator?
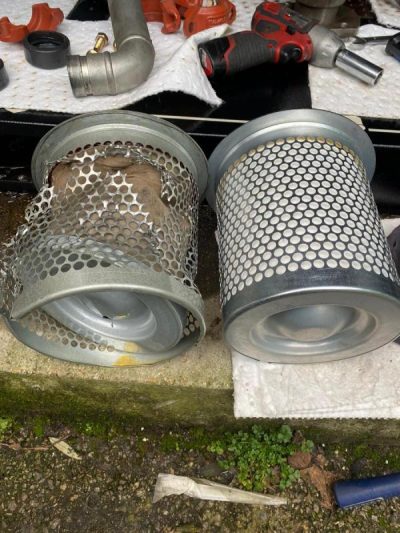
An Oil Separator does exactly what its name tells you… it’s a filter within an air compressor system that separates oil from the compressed air to protect systems components and your equipment at the end of the line.
Lubricated rotary air compressors mix oil with the intake air to lubricate the compressor.
Air-oil Separators, typically used on rotary compressors, are located just after the compressed air leaves the compressor, installed in the compressors discharge line. The Oil Separator ensures your compressors oil is recycled back into the compressor to keep it lubricated, whilst helping to ensure the compressed air exiting the compressor is free of oil.
Of course not all the oil will be removed, as some traces of oil and vapours may pass through the air filter material and remain in your air supply. Therefore, it is important you have other filters in place downstream to ensure these do not reach your devices.
We often get calls from customers saying they have oil ”down the line” and in their pipework. There can be numerous reasons for this but one of these causes can be that the air/oil separator has failed. If you look at the picture you can see the results of a failed separator. Although this is a rare occurrence, regular preventative maintenance can avoid this issue.
Caring for your compressor and doing necessary routine maintenance will help you save money in the long run. Air4U group can assist with preventative planned maintenance. Please check out our blog https://www.air4ultd.co.uk/service-and-maintenance/
Alternatively, if you wish to find out any further information or would like to book a service, please follow the link to send us an email at sales@air4ultd.co.uk
Oil and Oil Filters
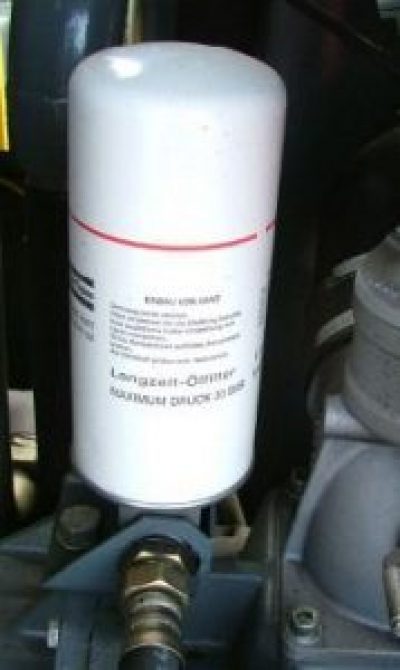
Protect your compressor, with the right air compressor oil filter, and save money on expensive repairs.
What does an air compressor oil filter do? They filter the oil to remove any dirt and dust. In other words: they protect your compressor from damage by contaminants. Dust and dirt will damage the filter element, wear the bearings and clog the oil-separator.
High quality oil filters are recommended to conserve this oil and also to protect other parts of the compressed air system. Just as with air cleaners and air/oil separators, the oil filters in a compressed air system are also part of a process chain, in which the weakest link can seriously lessen the performance of the whole system. If the oil filter does not work properly, the dirt deposits will negatively affect the air/oil separators, fine filters and machine components. The result is a considerable shortening of the filter service life and increased maintenance costs for the compressor.
Why Is It Important to Change Oil?
Oil performs a vital function for an air compressor. This specially formulated oil acts as a cooling, lubricating and sealing agent during compression. The lack of oil can lead to quick heating of your air compressor which, in many compressor models, causes an automatic shutdown. Thus, having the necessary amount of the correct grade oil allows your compressor to perform much longer.
Since compressor oil also acts as a sealant, its absence can cause leakage which greatly reduces its efficiency and the maximum pressure it produces. Moreover, the oil serves as a lubricant that prevents the wear and tear of compressor parts.
How Often Should We Change Compressor Oil?
The frequency at which one should change the oil in an air compressor heavily depends on the type of compressor you bought. Some compressors may need oil to be changed more frequently than others. The best source of information about this is found in the user’s instructions manual that comes with the compressor oil package you have purchased. Some instructions manuals even provide information about the expectancy life of the oil in terms of service hours.
If you are unable to locate your user’s manual, there are some basic guidelines for compressor oil changes. For Screw & Vane Compressors – Typically change standard oil every 2000 service hours. Some manufacturers offer an extended service life oil.
As mentioned, the need for oil change in an air compressor varies according to its model and service hours. At the least, you should change the oil in your air compressor once a year.
What Type of Compressor Oil Should Be Used?
Just like in oil change frequency for air compressors, it is always best to follow the recommendations of the manufacturer. Not only will it work best for your compressor, but it will also ensure that your warranty is not voided. When you are uncertain of what to use, especially when the user’s manual is nowhere to be found, Air4U Group can advise the correct oil for your machine.
Compressor oil is specially formulated for compressors, using motor oil or standard hydraulic oils can have a detrimental effect on your compressor performance and life cycle
Some compressor owners are also torn between using synthetic or standard air compressor oil. Both can be used if your manufacturer allows it, otherwise, it is best to stick to what is recommended to avoid voiding your warranty.
Standard air compressor oil is best for compressors that are not heavily used.
For heavy duty compressors like those used in construction areas or large industries, a synthetic compressor oil is more recommended. This type of oil can best protect the compressor from overheating and has a wide range of temperature suitability for colder environments. Many compressor users also say that synthetic compressor oil causes the compressor to run smoother and more quietly.
Where to Buy Compressor Oil?
To make sure that you are getting the best quality compressor oil, whether standard or synthetic, make sure to buy from trusted distributors. Air4U stock a wide range of oils suitable for most types of air compressors.
Caring for your compressor and doing necessary routine maintenance will help you save money in the long run. Air4U group can assist with preventative planned maintenance. For more information, please see our Blog about Maintenance and Service, https://www.air4ultd.co.uk/service-and-maintenance/