Common Air Compressor Problems
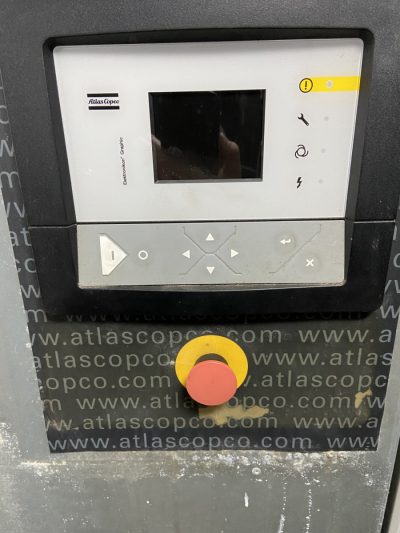
We often get phone calls from companies who are having a problem with their air compressor, which can easily be resolved with a quick chat with our Engineers. In this blog, we are going to let you know some of the most Common Air Compressor Problems and how you can fix it quickly, which could save a phone call.
The Air Compressor not starting.
A common problem is when you can not get your Air Compressor to start at all. There are a few reasons why this can happen, so it is easiest to run through this trouble shooting list from the simplest to most difficult fix.
No Power
Check and make sure the compressor is plug in and power is on. Check the mains and control fuses, replacing if necessary. It it is still not working, press the reset button.
Emergency Stop Button
Believe it or not, we are regularly called out because customers have pressed the 'EMERGENCY STOP' button to switch the compressor off, rather than the stop button. The 'EMERGENCY STOP' button remains latched in. The compressor is vented and the machine is prevented from re-starting.
You need to turn the 'EMERGENCY STOP' button in the direction of the arrow to unlatch it. Press the 'Reset' key to delete any existing alarm messages and switch the machine on.
Low Oil
It is easy to forget to change the oil on an air compressor, but the results can be dramatic. This is why we always recommend a regular service schedule. If your air compressor will not start, and the power is not a problem, check and top-up the oil.
Overheating.
Air compressors overheating is one of the most common causes of failure, even with compressors that might otherwise last for many additional years. So, what could be the cause of the compressor overheating?
Plant Room Temperature.
If direct sunlight falls on your air compressor, and there is inadequate ventilation around it, this can make your compressor to overheat. As a general rule, air compressors are designed to operate in an environment where the temperature remains between 5'C and 40'C. Normally, the maximum ambient temperature of the room that a compressor is in must be lower than 40'c to 45'C, even at the hottest times of the day.
Compressors with no ducting will exhaust hot air into the room, heating up the space if there is not adequate air flow/ventilation (both into and out of the room). In the worst case scenario, the compressor's cooling fan will suck in the already heated air, which will form a circuit of recycled exhaust air. This will quickly cause the compressor to overheat.
Low compressor oil levels can lead to overheating.
You should check your oil level on a regular basis to ensure that there is sufficient oil for the compressor to operate efficiently. Oil lubricated compressors pass small amounts of oil during operation. If the oil level is too low, the machine will not have a proper flow through the cooler. Thus, is could easily overheat. Check your air compressor oil at least once a week to make sure that it is at the correct level. The manufacturer's manual has instructions for proper oil check procedures. Our Engineers will also top-up the oil during any preventative maintenance visits as necessary. We keep most types of compressors oil in stock if required.
Blocked Coolers.
If the compressor operating temperature is too high, it may be that the Cooler (or radiator) could be dirty. A quick fix is to blow the cooler out in the reverse direction of the air path to get your machine up and operational. To do this, you can blow cool air through the cooler. You can use a reduced pressure blow gun or air line to do this. If the pressure is too high, you can damage the cooler.
If it is beyond this point, the fix may involve removing the cooler to have it properly steam cleaned. During a preventative maintenance visit, our engineer will clean the cooler as required.
Thermostat.
The thermostat or thermostatic valve is one of the most vital compressor parts. It enables the system to measure and respond to changes in the air temperature inside the unit by controlling the flow of oil, keeping your air compressor running smoothly and effectively.
Thermostatic valves sense the temperature of the oil and decides how much cooling/heating is necessary.
When the compressor oil is cold, the valve by-passes the oil cooler, so no oil flows through the cooler. This is done to heat up the oil as soon as possible, to remove any water condensate. Low temperatures are the number 1 enemy of screw compressors.
The oil can often be very hot, which results in the compressor will shutting down or tripping out. To re-use the oil for additional cooling, it must pass through an oil cooler before re-entering the compressor.
If you have tried these quick fixes and still need help, just call our team of engineers on 01903 257112 or please follow the link to send us an email at service@air4ultd.co.uk