Do you need a Backup Air Compressor?
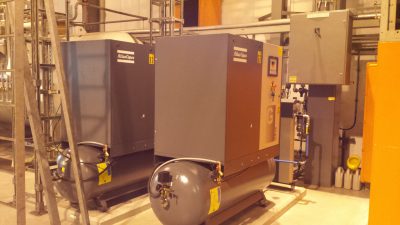
It might not seem to be common sense that reducing total operating costs and increasing the overall reliability of your compressor system could require adding more machinery. If you only have one compressor and that compressor must undergo routine maintenance or you have a breakdown and require emergency service, what happens to your production? It grinds to a halt, leading to costly downtime and a substantial loss in revenue.
Avoid this possibility by investigating a few of the backup options below:
Backup Compressor.
Having a backup compressor eliminates losses of production. If one compressor fails, the backup compressor is ready to be brought into operation.
Lead and Lag.
One compressor is assigned to be the “lead” compressor, while the other is designated as the “lag” compressor. When the lead compressor’s pressure drops to a predetermined point, the lag compressor takes over.
Create Redundancy.
A second air compressor can be linked to operate alongside your main compressor. Both compressors will be sharing the demand, and if the lead compressor fails, the lag unit will continue to operate. This strategy minimizes wear and tear on both units.
Investing in a second compressor is essentially an insurance policy. Your main compressor has a lot of responsibility, so leaving things to chance? Not the wisest option.
Air compressors are highly-engineered products that are essential for production in millions of businesses globally. In fact, compressed air is so critical to these facilities that it is often called the “fourth utility”! Most production cannot function without their utilities such as electric, water, and gas – and it stands to reason that this is also true of compressed air. The cost of downtime of this utility needs to be considered in your air system. Is it important enough to justify a backup unit? Does the backup just sit around and ‘do nothing’?
Are Backup Air Compressors Essential?
The answer is simple: if your business is heavily reliant on compressed air to operate, production will cease, leading to a loss in output, possible production line losses, and costly downtime. Keep in mind that it could be a long time before a compressed air service technician reaches you to complete the repair! And without a backup compressor available for immediate use, the time, money, and productivity lost in the interim between unexpected shutdown and being back up-and-running can be extremely detrimental to the business’ bottom line.
It’s unfortunate, but even the best equipment fails.
This means that having a compressor system, complete with a backup compressor, is absolutely critical. Being proactive and purchasing one now, rather than down the road, is the smartest business decision – especially when you weigh the costs versus consequences of not having one. An additional benefit? Having backup compressors means that maintenance can be done at virtually any point in time, rather than after hours or during the holidays or weekends when production isn’t occurring!
The worry of the compressor sitting and doing nothing can also be eliminated by load sharing. This allows cycling of the compressors to allow even running time for each. Simple controls evenly allot run time allowing each machine to spread the work and maintenance cycles more efficiently for your business while still protecting production uptime.
So, to summarize, the reasons that you need a backup air compressor are:
- To minimize any negative impact on production brought on by unexpected downtime.
- Schedule maintenance on your primary compressor at any point in time.
- Using both your primary air compressor and backup air compressor in your application through load sharing.
Essentially, the costs of not investing in a backup air compressor far outweigh the cost of purchasing one, and you can take surprise shutdowns off the worry list. Rest easy and avoid unplanned chaos – discuss investing in a backup compressor today, please do not hesitate to follow the link to send us an email at sales@air4ultd.co.uk