Energy savings with Heat Recovery
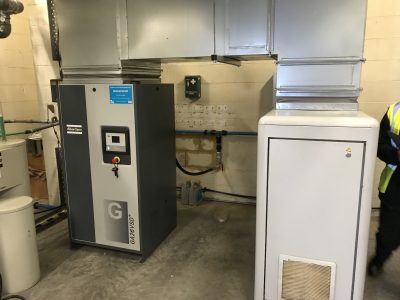
Heat Recovery helps to reduce energy consumption, eliminate emissions and can save money
Compressed air is one of the most important utilities for the industry. It is also one of the largest consumers of energy. Therefore, compressor energy savings have a significant impact on costs and on the environment.
Most responsible Compressor manufacturers provide various solutions in this regard, such as Heat Recovery with Rotary Screw Compressor Systems for example.
Compressors primarily generate heat. Unbelievable as it may seem, up to 94% of the electrical energy input to a compressor is turned into heat. The action of compression charges the air in the compressor with potential energy. This energy is given up at the point of use by the compressed air expanding and drawing heat from the surroundings. Statistics show that compressed air typically accounts for about 12% of the total energy costs for industrial manufacturers.
Without energy recovery, this heat is lost into the atmosphere via the cooling system and radiation. However, the good news is that between approximately 70% of energy is recoverable from oil-injected screw compressors, and up to 94% from oil-free water-cooled screw compressors.
Heat recovery methods.
Compressor users wanting to improve the efficiency of their compressed air system can choose from a number of heat recovery methods:
Air Heating.
The simplest and most direct method of recovering the heat generated in a fluid-/oil-cooled rotary screw compressor is by using the heat from the compressor system's warmed cooling air. This heated air is ducted away to be used for space heating of warehouses and workshops. The hot air can also be used for other applications such as drying, heat curtains and pre-heating combustion air. When the hot air is not needed, a manual or automatic flap, or louvre discharges it outside into the open. The flap can even be thermostatically regulated to maintain a constant, set temperature. The space heating method allows 94 % of the electrical energy consumption of a screw compressor to be recovered and it is well worth it.
Hot water.
Hot water for various purposes can be recovered from either an air-cooled or water-cooled compressor package by means of a heat exchanger installed in the air end cooling oil circuit. Plate or fail-safe heat exchangers are used, depending on whether the water is used for heating, laundry or even showering, production or commercial cleaning purposes. Water temperatures of up to a maximum of 70 °C can be achieved with these heat exchangers. Experience shows that for compressor packages upward of 18.5 kW capacity the additional costs for these heat recovery systems can in some cases be paid back within two years.
Normally, we recommend the compressor's primary cooling system should never be used both for cooling and as a heat recovery system. The reason being should the heat recovery system fail then compressor cooling and therefore the production of compressed air would be endangered. The safest method is to fit an additional heat exchanger in the compressor purely for heat recovery. Then, in the event of a failure, the compressor can revert to its primary air- or water-cooling system and so continue operation. The supply of compressed air is ensured.
Recovering the heat of compression for a useful purpose is an intelligent way of improving the economics of compressed air production and benefitting the environment at the same time. The effort involved can be comparatively small. The investment is quickly recovered depending on local circumstances, how you use the heat generated and the method of recovery chosen.
If you would more information or advice, please do not hesitate to follow the link to send us an email at sales@air4ultd.co.uk