Find and Fix that Leak
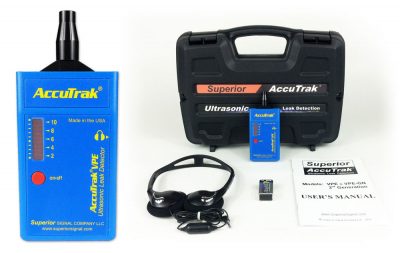
All compressed air systems have leaks. Leaks are often ignored since they are not an immediate health and safety hazard but reducing air leaks is the single most important energy saving measure you can take.
Leaks are a significant source of wasted energy. It’s not uncommon for 20-30% of the compressor’s output to be wasted. A typical poorly maintained plant will have a leak rate equal to 20%+ of total compressed air production capacity. On the other hand, proactive leak detection and air compressor repair can reduce leaks to less than 10% of output.
As you know, leaks are worse with higher pressure. By reducing system pressure, your system will require less energy and also lower the leakage rates. Plant header pressures should be as low as possible to support the process because it minimizes compressor energy use and leakage.
Compressed air leaks can contribute to problems with system operations, including:
- Fluctuating system pressure can cause air tools and other air-operated equipment to no function correctly, negatively affecting production.
- Excess compressor capacity, resulting in higher than necessary costs.
- Decreased service life and increased maintenance of supply equipment (including the compressor package) due to unnecessary cycling and increased run time.
- a noisy environment for staff.
Common leakage sources are:
- Air-using equipment left running when not needed
- Quick Release Couplings
- Hoses
- Tubes
- Fittings
- Pipe Joints
- FRLs (filter, regulator, lubricator)
- Condensate Traps
- Valves
- Flanges
- Packing
- Thread Sealant
- Point-Of-Use Devices
Identifying and Measuring leaks
Initially conduct an out of hours survey and walk the site listening for leaks, when the whole plant is sufficiently quiet that large leaks can be audible. Smaller leaks can be below the threshold for hearing and therefore the absence of the hiss of leaking gas does not mean that there are no leaks. Since air leaks are almost impossible to see, other methods must be used to confirm their location. Ultrasonic leak detection is probably the most versatile form of leak detection, but you can also use a soap solution brushed onto pipe fittings and look for bubbles, or a leak detection spray.
Handheld ultrasonic leak detectors are the best way to detect leaks whilst production is running. (Be aware that some dryer types have purge cycles which use air as part of their function).
Once you have identified where there are leaks, we can help. Our compressed air team can repair problem areas. We can assess your system to ensure your air compressors, dryers, storage, regulators, distribution and point of use equipment is right for your application.
As part of a good practice, we recommend compressed air users implement a leak management programme as follows:
- Tag the leaks and record on a site plan
- Grade the priorities - it could be as simple as 1,2,3
- Fix the largest leaks first
- Encourage users to report leaks
- Repair all leaks as soon as practicable
Regularly monitor your system
Leaks need to be monitored constantly. To minimise losses, carry out a leak survey at least twice a year to keep the problem under control. If you have insufficient in-house resources, we can offer a leak management service.
Top Tips
- Have an ongoing leak test and repair programme.
- Leaks reappear and a 3mm hole could cost over £600/year in wasted energy.
- And finally...
- Once you have repaired the leaks, check the pressure drop from the compressor to points of use as you may be able to reduce the generation pressure at the compressor.
- Otherwise, fixing leaks could increase the pressure and the predicted savings will not be realised.
- Also, the increased pressure could create more new leaks.
- Ensure you maintain the whole system
Effective maintenance is essential to energy efficiency. Cutting back on maintenance is a false economy, because doing so increases the energy consumed, decreases service life, and reduces equipment reliability.
In order to monitor the leakage rate, consider installing permanent flow metering. This is also an effective way of identifying any changes in consumption which need further investigation.
Pressure Systems Safety Regulations 2000 (PSSR)
In addition, the law requires all systems operating at greater than 0.5 bar with an air receiver installed, to comply with the Pressure Systems Safety Regulations 2000 (PSSR). Regulation 12 of the PSSR requires that compressed air equipment be properly maintained to minimise health and safety risks associated with a pressurised system.
Check out our News Blog regarding this: https://www.air4ultd.co.uk/what-is-a-written-scheme-of-examination/